Erfurter Rapid.Tech – ein Stück näher an der Zukunft
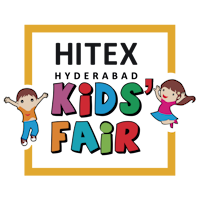
12.06.2013 08:47:24, Hyderabad International Trade Expositions Ltd.
Überzeugen konnte die diesjährige Rapid.Tech, die am 14. und 15. Mai zum zehnten Mal in Erfurt stattfand, nicht nur durch das deutliche Besucherplus von 18 Prozent. Auch Inhalte und Qualität der Vorträge von 70 renommierten Referenten aus zehn Ländern machten deutlich: An additiven Fertigungsverfahren kommen zukunftsorientierte Unternehmen nicht mehr vorbei. Parallel zur Jubiläumsveranstaltung der Kongressmesse für Additive Manufacturing (AM) feierte die FabCon 3.D Premiere. Hier wurden 3D-Drucker für Endverbraucher präsentiert, die auf ein enorm großes Interesse stießen.
Bei der ersten Rapid.Tech 2004 war Additive Manufacturing noch eine Nischentechnologie, inzwischen schätzen Experten das weltweite Marktvolumen auf 2,2 Milliarden Dollar pro Jahr – mit stark steigender Tendenz. Und nicht nur das, sie gehen auch davon aus, dass sich durch additive Fertigungsverfahren die Art des Produzierens in den kommenden Jahren stark verändern wird. Dafür spricht auch das enorme Potential, das Additive Manufacturing für eine schnellere, wirtschaftlichere und nachhaltigere Fertigung bietet. Einen Vorgeschmack auf diese bevorstehende „industrielle Revolution“ gab die diesjährige Rapid.Tech, die mit insgesamt 1.532 Tagungsteilnehmern und Messebesuchern ein Plus von 18 Prozent verzeichnete. Sie reisten aus 16 Ländern an, wobei nicht nur Europa, sondern auch Nordamerika sowie Asien vertreten waren. Dies sorgte bei den 70 ausstellenden Unternehmen aus fünf Ländern, die Verfahren, innovative Maschinen, Materialien und Dienstleistungen präsentierten, für beste Stimmung: „Wir sind sehr zufrieden mit dem Verlauf der Messe, mit der Qualität und Quantität der Kontakte, die wir hier auf der Messe knüpfen konnten. Es sind überwiegend fachkundige Besucher aus Branchen wie beispielsweise Luft- und Raumfahrt, Dentaltechnik, Formen- und Werkzeugbau, die mit konkreten Fragen zu uns kommen. Wir hatten aber auch Vertreter aus Unternehmen hier, die sich über die Technologie informieren, weil sie ihre Produktion auf die Zukunft ausrichten möchten“, berichtet Stephan Wein, Gebietsverkaufsleiter bei der EOS GmbH. Mit Anwendertagung, Konstrukteurstag, den Fachforen Luftfahrt, Medizintechnik und CAD/CAM und Rapid Prototyping in der Zahntechnik sowie dem Forum der Fraunhofer-Allianz Generative Fertigung bot die Rapid.Tech 2013 ein Tagungsangebot zu AM, das in dieser Art einzigartig ist. Es ermöglichte sowohl Einsteigern als auch Experten sich gezielt zu informieren und Erfahrungen auszutauschen.
Fahrzeugentwicklung – schneller, kosteneffektiver und produktionsunabhängiger
Welche Potentiale sich durch AM beziehungsweise Rapid Prototyping bei der Entwicklung und Herstellung exklusiver Fahrzeuge ergeben, beleuchtete David Hayward, Operations Manager Design Studio bei der Bentley Motors Ltd. und Keynote-Speaker der Rapid.Tech. Das Design Studio arbeitet seit zehn Jahren mit generativen Verfahren. Anfangs wurden sie nur für wenige Teile wie beispielsweise maßstabsgetreue Räder oder Innenraum-Bauteile eingesetzt. Die Weiterentwicklung bei Maschinen und Materialien ermöglicht heute dagegen die Herstellung einer Vielzahl von Interieur- und Exterieurkomponenten für maßstabsgetreue Modelle (1:3 und 1:10), unter anderem Außenspiegel, Schweller, Scheinwerfer, Kühlergrill, Schalter und MMI (Multi Media Interface)-Einheit, durch AM. Dabei lassen sich unterschiedliche Designvarianten innerhalb weniger Stunden herstellen und greifbar bewerten. Da für eine solche Modellherstellung früher Tage, Wochen oder sogar Monate erforderlich waren, entstanden Designalternativen nur auf dem Papier. Qualität und Optik der generativ gefertigten Modellteile entsprechen nahezu den späteren Serienteilen. Gleichzeitig steigt die Designfreiheit, da sich der Designer nicht mehr mit der späteren Produzierbarkeit der Teile beschäftigen muss, sondern einfach kreativ sein kann. Der Einsatz von AM kann auch zu einer Verkürzung der Designphase für neue Modelle beitragen. Ein weiterer Vorteil liegt in der Möglichkeit der Individualisierung von Komponenten und Ausstattungsdetails entsprechend den Kundenwünschen. Inzwischen werden im Design Studio des Herstellers exklusiver Fahrzeuge aber nicht nur Automobilteile in AM entworfen, sondern auch individuelle Produkte wie etwa Brillen oder Schmuck für Bentley Kunden. Für David Hayward gibt es auch keinen Grund, dass Automobile eines Tages nicht komplett durch generative Fertigungsverfahren produziert werden – zumindest bei kleinen Serien. Denn in Formel-1-Fahrzeugen und in der Luftfahrt haben AM-Komponenten bereits bewiesen, dass sie ebenso robust und leistungsfähig sind wie konventionell hergestellte Bauteile. Verändern kann AM, so Hayward, letztendlich auch die Teile-Logistik in der Automobilproduktion: Zulieferer werden nicht mehr Teile in ein Werk anliefern, sondern Maschinen an den Produktionslinien stehen haben.
Anwendertagung – AM-Bauteile prozesssicher produzieren
Unabhängig in welchem Verfahren Serienteile hergestellt werden, Reproduzierbarkeit ist eine entscheidende Anforderung. Dies war eines der Hauptthemen der zweitägigen Anwendertagung. In den Vorträgen wurden unter anderem Konzepte für die Prozessführung und Baustrategien sowie neue Entwicklungen bei Lasern zur Herstellung komplexer Bauteilgeometrien und Maschinen thematisiert. Es ging auch um die Einflüsse der Prozessparameter Scangeschwindigkeit, Laserleistung, Bahnabstand auf die technologischen Eigenschaften und Qualität von strahlgeschmolzenen Teilen sowie die Ursachen für eine mangelnde Reproduzierbarkeit beim Lasersintern von Kunststoffbauteilen. Dazu stellten verschiedene Referenten Lösungen zur Prozessüberwachung beziehungsweise Prozessoptimierung vor. Antonio Amado (Inspire AG, irpd) beschäftigte sich in seinem Referat mit der Fließfähigkeit von Polymerpulvern für das Selektive Lasersintern bei höheren Temperaturen und präsentierte neueste Erkenntnisse: Der dynamische Lawinenwinkel, das Volumenexpansionsverhältnis und die Unebenheit der Oberfläche nach dem Lawinenereignis (surface fractal) stellen geeignete Parameter zur Qualitätskontrolle von kommerziellen SLS-Pulvern und zum Screening während früher Pulverentwicklungsphasen dar.
Die Freiheit des Designs konstruktiv optimal nutzen
Die Designfreiheit, die AM und Rapid Prototyping Konstrukteuren bietet, ist nahezu grenzenlos. Dass bei aller technologischen Freiheit die Schutzrechte Dritter nicht aus dem Fokus geraten dürfen und dadurch der Richter zum Produktionsleiter wird, machte Professor Dr. Lambert Grosskopf (LL.M. Eur., Universität Bremen) zu Beginn des Konstrukteurstags deutlich. Im Mittelpunkt der weiteren Vorträge der eintägigen Veranstaltung standen die Besonderheiten bei der Umsetzung von Produktideen mit AM sowie erfolgreiche Anwendungen unter konstruktiven und werkstofftechnischen Gesichtspunkten. Markus Hatzenbichler (TU Wien) stellte in seinem Vortrag einen Verfahrensvergleich von DLP-basierter Stereolithographie und dem selektiven Laserschmelzen an und zeigte entscheidende Unterschiede dieser Technologien bei der Herstellung keramischer Bauteile auf. Der Vortrag informierte darüber hinaus über Aufbereitungsmethoden für keramische Pulver.
Personalisierte Implantate und künstliche Blutgefäßsysteme für die Praxis
In seinem Keynote-Vortrag zur Medizintechnik beleuchtete PD Dr. med. Horatiu Rotaru, (Universitätsklinik Cluj-Napoca; Rumänien) die lange Entwicklung der Cranioplastik und die enormen Fortschritte, die durch personalisierte, in generativen Verfahren gefertigte Implantate heute erzielt werden. Die Möglichkeiten sind aber nicht nur auf die „Reparatur“ von Schädeldefekten begrenzt, wie die Referate des zweitätigen Medizintechnik-Fachforums belegten. So informierte Dr. Raimund Jäger (Fraunhofer IWM, Freiburg) über die Fertigung eines verzweigten Blutgefäßsystems, das potenziell als Versorgungssystem für ein Gewebemodell oder ein Transplantat verwendet werden kann. Er betonte, dass dabei die Zusammenarbeit eines multidisziplinären Teams aus Produktionstechnologen, Chemikern, Biologen und Werkstoffwissenschaftlern unverzichtbar ist und beschrieb die Vorgehensweise zur optimalen Auslegung des Systems. In einem ersten Schritt wurde die optimale Topologie des Aderbaums ermittelt. Danach erfolgte die Untersuchung der Flussbedingungen in Verzweigungen und deren lokale geometrische Optimierung, die die Endothelialisierung (Bildung neuer Gefäßinnenhaut) der Gefäßwand fördert.
In der Luftfahrt den Strukturen der Natur folgen
AM ist in der Luftfahrt seit 2002 etabliert und eröffent durch die fortschreitende Entwicklung bei Maschinen und Materialien neue Potenziale, wie Professor Claus Emmelmann (Laserzentrum Nord) im Keynote-Vortrag zu aktuellen Trends und Entwicklungen des AM in der Luftfahrt berichtete. Dazu zählen gewichtsoptimierte Einzelkomponenten sowie integrale Baugruppen und leichtere Großstrukturen. Dabei ermöglichen additive Verfahren die belastungsgerechte Auslegung der Komponenten, deren Strukturen sich an Vorbildern aus der Natur, beispielsweise einem Kornhalm, orientieren sowie deren wirtschaftliche Herstellung. Ansätze dazu boten beim zweitägigen Luftfahrt-Fachforum die Vorträge zu neuesten Entwicklungen und Anwendungen der Technologien Fused Deposition Modeling (FDM), Lasersintern (LS) und Selective Laser Melting (SLM). Klas Boivie (SINTEF Raufoss Manufacturing AS, Norwegen) beschrieb in seinem Referat die Prinzipien und Verifizierung eines möglichen Hybrid-Produktionsprozesses. Es werden dabei auf ein konventionell gefertigtes, rohrförmiges Bauteil zwei Halteklammern aus Werkzeugstahl mittels AM direkt additiv gebaut. Die Fallstudie zeigte, dass es grundsätzlich möglich ist, hochbelastete Bauteile für Luftfahrt- und andere Anwendungen in Hybrid-Produktionsprozessen herzustellen. Mit völlig anderen, aber ebenso interessanten Herausforderungen beschäftigt sich Part-Time-Scientists. Dahinter verbirgt sich ein internationales Team, das im Rahmen des Google Lunar X-Prize Wettbewerbs am Wettlauf zum Mond teilnimmt. Für diese Mission entwickeln die Teilzeitwissenschaftler unter anderem den Mond Rover „Asimov“. Um neue Technologien einerseits schnell auf ihre Integrationsfähigkeit in das Gesamtsystem testen zu können, arbeiten die Teams mit AM-Funktionsprototypen. Im weiteren Verlauf ist der Einsatz von FDM. Du Laserschmelzbauteilen als echte Bauteile im Mondrover geplant – erste Komponenten liegen schon für Tests vor. Besonders geeignet sind diese Fertigungsverfahren aufgrund der Möglichkeit von Funktionsintegration. Darüber hinaus sind die AM-Bauteile robust – und das müssen sie auch sein, denn die Bedingungen auf dem Mond sind schon aufgrund der enormen Temperaturschwankungen sehr hart.
Dentale Fortschritte von der Abformung bis zur Frästechnik
Sowohl in der Zahnarztpraxis als auch im zahntechnischen Labor etabliert sich die digitale Technik mit Riesenschritten. Das Fachforum „CAD/CAM und Rapid Prototyping in der Zahntechnik“ informierte an zwei Tagen in 13 Vorträgen über den aktuellen Stand und neueste Entwicklungen. Dazu zählte auch ein völlig neues Abformkonzept, das Wilhelm Kiefer (Dental Kiefer) präsentierte. Es basiert auf dem Twin-Jection-Löffel, in den 19 Minikameras integriert sind. Das System ermöglicht innerhalb von rund zwei Sekunden die Aufnahme aller Zähne eines Kiefers. Die Position der Kameras und ihr Abstand im Löffel zueinander ist klar definiert, was die Errechnung STL-tauglicher Daten ausgesprochen einfach macht. Für die Modellherstellung stehen spezielle Basen inklusive Software zur Verfügung. Der Zahnkranz lässt sich virtuell in Idealposition über der jeweiligen Modellbasis platzieren. Anschließend kann das Modell digital gedruckt oder konventionell gefräst werden. Durch die Visualisierung realer Kaubewegung die Funktion sicherstellen sowie gleichzeitig die Stabilität verbessern und damit Komfort und Qualität von Zahnersatz optimieren. Einen Lösungsansatz dafür stellte Sebastian Ruge (Universität Greifswald, Abteilung CAD/CAM und CMD-Behandlung) mit dem 3-D-Virtual Articulation System (3D-VAS) vor. Mit dem gemeinsam von der Universität Greifswald und der Zebris Medical GmbH entwickelten System lässt sich die Okklusion (Kontakt zwischen den Zähnen des Ober- und Unterkiefers) bei Kaubewegungen virtuell darstellen. Neue Möglichkeiten in der Frästechnik zur Modellherstellung waren das Thema des Vortrags von Sandra Häge-Betz (MB Maschinen GmbH). Sie erläuterte dabei, dass die Gesamtheit des Prozesses in Zukunft immer wichtiger wird und die Betrachtung auch in der Herstellung der Modelle darauf gezielt ausgerichtet werden muss. Dies ermöglicht ein neues System für die Modellherstellung mit einem Nullspannsystem. Diese Alternative zur Stereolithographie und zum Modellfräsen aus Ronden-Rohlingen bietet Vorteile wie Kostensenkung, Oberflächengenauigkeit, Einbindung in zukünftige Be- und Verarbeitungen, beispielsweise die Implantatplanung.
Die Zukunft ist generativ – nicht nur beim Forum der Fraunhofer-Allianz Generative Fertigung
Mit Konzepten für die generative Fertigung von morgen beschäftigte sich das Forum der Fraunhofer-Allianz Generative Fertigung – unter anderem im Vortrag von Claus Aumund-Kopp und Juan Isaza (Fraunhofer IFAM). Sie wagten einen Blick auf den Einsatz generativer Fertigungstechniken im Jahr 2025. Am Beispiel eines Elektrofahrzeugs – dann bereits ein Oldtimer – erläuterten sie, wie Schadensanalyse, Bauteilproduktion und Ersatzteilaustausch zu einem ökonomisch und ökologisch optimierten Gesamtkonzept verschmelzen. Ob es noch bis 2025 dauert, bis das Thema des Referats von Kamilla König-Urban und Benjamin Graf (Fraunhofer IPK) Realität wird, ist fraglich. Nach dem Vergleich der Eigenschaften der generativen Verfahren Selektives Lasersintern und Pulver-Auftragschweißen demonstrierten sie Anwendungen für industrielle Reparaturaufgaben. Dazu zählten die Reparatur flächiger und volumenförmiger Defekte auf einer generativ gefertigten Turbinenschaufel und die Reparatur von Rissen beispielsweise in Gehäusen durch das Laser-Pulver-Auftragschweißen.
Mit Schuhen zum ersten Preis
Der Student Design & Engineering Award for Rapid Manufacturing, mit dem die Messe Erfurt innovative und mit additiven Fertigungsverfahren verwirklichte Ideen auszeichnet, wurde in diesem Jahr zum siebten Mal vergeben. Das hohe Maß an Kreativität und Individualität, das die eingereichten Arbeiten auszeichnete, machte es der Jury nicht leicht, die Gewinner zu ermitteln. Beim dritten Preis, einem Gutschein der Alphacam GmbH, entschied sich die Jury für das AM-Kunstwerk „Vergangenheit berührt Gegenwart“ von Marcel Karnapka. Mit additiv gefertigten Fahrradkomponenten sicherte sich Ralf Holleis den zweiten Preis, einen Bauraum auf der EOS Formiga der EOS GmbH. „MINE 3D-gedrckte Schuhe“ nannte Elena Gerber ihre Arbeit. Und diese Schuhe waren so unwiderstehlich, dass sie dafür mit dem ersten Preis, einem Cube 3D-Printer der 3D-Systems GmbH, ausgezeichnet wurde.
Bei der rasanten Entwicklung, mit der AM die Produktion in vielen Branchen verändert, bleibt es spannend zu sehen, welche Themen bei der 11. Rapid.Tech im Frühjahr 2014 auf dem Programm stehen werden.
1st Floor, Trade Fair Office
500084 Hyderabad
Indien
-
www.hitex.co.in
Hyderabad Kids' Fair Hyderabad
31.01.2025 - 02.02.2025
für Fachbesucher und Privatbesucher
jährlich